High Reliability Organizations (HROs) approach harm and the risk of harm differently, with the goal, plan, systems, and mindset that only Zero Harm is acceptable.
Learn more in this video by Tony Milian, formerly a Senior Advisor with Value Capture.
You can also listen to Tony talk about these concepts in an episode of our Habitual Excellence podcast. A transcript of this video also follows, below.
Podcast Episode with Tony
Listen to the episode:
Video Transcript:
Tony Milian: Hello, and thank you for joining me in this brief overview of a key characteristic shared by High Reliability Organizations. In this video we're going to cover the topic of preoccupation with failure.
My name is Tony Milian, and I'm a senior advisor with Value Capture. We help healthcare organizations capture dramatically more value through achieving perfect care and perfect safety for patients and staff.
In the healthcare industry, many of us have heard about the concept of high reliability organizing. So what is a high reliability organization, and why does it matter to you as a healthcare professional?
What are High Reliability Organizations?
High Reliability Organizations are organizations that operate in complex high hazard domains for extended periods without series accident or catastrophic failures. Industries with great examples of High Reliability Organizations include transportation, particularly train travel and air travel, nuclear power, manufacturing, emergency services like fire and forest fire services, and even some extreme sports like skydiving.
To better understand the impact of high reliability organizing, let's make a brief comparison of the employee safety record of Alcoa, the world's leading manufacturer of aluminum, to the average American hospital.
Alcoa, the world's largest aluminum manufacturing company, an organization that mines, moves, and manufactures metal that's heavy and hot, has managed to maintain a long term safety record for employees that averages 1.12 recordable injuries per 100 full time employees. That's 1.12 recordable injuries for every 200,000 hours worked.
By contrast, the average American hospital averages 6.8 recordable injuries per 100 full time employees.
When looked at in terms of days away restricted or transferred, meaning that the employee had to take time off of work, restrict work activities, or was permanently transferred to a new role to accommodate their injury, Alcoa performed 17 times better than the average American hospital.
Let's make a similar comparison with regards to customers of high reliability organizations and healthcare organizations.
The airline industry is another great example of high reliability organizing. In 2019, there were only 25 fatal airline incidents out of 39 million total flights flown. By contrast, American hospitals admitted just over 36 million patients in 2019. Patients experienced approximately 1.7 million hospital acquired infections in that same time period.
By comparison, the airline industry had .000005 percent accident rate versus hospital acquired infection rates per admission of 4.7 percent.
Based on these statistics, it's clear that High Reliability Organizations have better safety records than the healthcare industry. But why is that? What are these organizations doing that sets them apart?
Preoccupation with Failure
One attribute that High Reliability Organizations share is something called a preoccupation with failure. Preoccupation with failure is the first principle of high reliability organizing.
How is preoccupation with failure defined? The Wiley Library defines preoccupation with failure in the following way.
"Preoccupation with failure, the first High Reliability Organization principle, captures the need for continuous attention to anomalies that could be symptoms of larger problems in a system. HROs are preoccupied with failure in three ways.
First, they work hard to detect small, emerging failures because these may be a clue to additional failures elsewhere in the system.
Second, HROs work hard to anticipate and specify significant mistakes that they don't want to make.
Third, HROs know that people's knowledge of the situation, the environment, and their own group is incomplete. When people look for failures, they acknowledge the existence of incomplete knowledge."
An Example
Let's use this pyramid to describe the difference between a High Reliability Organization preoccupied with failure and organizations that might respond to safety issues once it reaches a certain level of severity.
The bottom of the pyramid and the number 10,000 represents the number of unsafe conditions and behaviors that may exist in an organization at any given time. As an example, let's assume that employees of company X walk down a sidewalk in front of their place of work daily. There's a hole in the sidewalk, and they step over the hole every single day.
As employees look at the hole they think to themselves, "That hole in the sidewalk is probably dangerous. One of these days, I'm going to notify the maintenance department so they can fix that hole."
Unfortunately, everyone else that steps over the hole thinks the same thing, but they don't report it.
Out of the 10,000 unsafe conditions or behaviors, 1,000 represents the number of near misses that may occur. In the case of the hole in the sidewalk, out of every 10,000 times employees walk over the hole, someone catches their foot about 1,000 times and nearly falls, but they don't.
Whenever a near miss occurs, the employees look back at the hole and think to themselves, "I really need to let maintenance know about that hole." But the day takes its course, and employees forget to report the hole to the maintenance department.
Unfortunately about 100 times out of every 10,000 unsafe conditions or behaviors encountered, an injury severe enough to result in physical harm occurs. In many cases, these injuries are minor and only require first aid, but they still result in physical harm.
In the case of the hole in the sidewalk, out of every 10,000 times employees walk over the hole, about 100 times they will trip, fall, and skin their knee or injure themselves in a minor way.
As a result, they have to receive first aid at their work clinic. In those incidents an accident report is filed, and maintenance is notified. As a result, the maintenance department puts in a work order and schedules a repair in their work queue.
About 10 times out of every 10,000 unsafe conditions harm is severe enough to result in an injury that requires medical attention and time away. These are called DARTs, or Days Away Restricted and Transferred.
In this case, 10 times out of every 10,000 times employees walk over the hole, they fall and sprain their ankle or break their wrist. In those situations, the employees leaves work to seek immediate medical attention, and afterwards, they have to take a few days off of work to recover and may need physical therapy sessions for a period of time to achieve full range of motion.
At this point, workforce health and safety files a report with Workers' Compensation. Maintenance is notified, and they prioritize fixing the hole in the sidewalk at the front of the queue due to the severity of the injury.
Unfortunately, in the worst of all situations about 1 out of every 10,000 unsafe conditions results in harm that is severe enough to result in permanent life altering injuries or in the most unfortunate of cases death.
In the example of the hole in the sidewalk, employees walk over the hole 10,000 times. But 1 time out of every 10,000 times they fall, hit their head, and injure themselves so severely that they experience permanent loss of motor skills and impair their ability to work.
Given the severity of the injury, the company closes work for two days and conducts a thorough investigation of the grounds to identify hazards that can result in falls. They find three such hazards and hire outside contractors to help their maintenance crew repair the hazards before people return to work.
Many organizations will respond to harm with a formal investigation and corrective action once harm has reached a 10 level. In some cases, organizations that are more proactive about safety will begin to investigate and take corrective action at the 100 level.
Healthcare organizations frequently fall into this category of response. This type of action is still reactive. Action only takes place when a harm has occurred. The trigger for action is the harm.
As we saw with the previous example of the hole in the sidewalk, however, the same underlying unsafe condition resulted in any number of harms, ranging in severity from a fall with cuts and bruises, all the way to life threatening and permanently life altering injuries.
What Would an HRO Do?
In High Reliability Organizations, by contrast, every employee is constantly on the lookout for unsafe conditions and behaviors. These conditions are seen as gems, because they help people within the organization identify vulnerabilities and processes, policies, physical space, and training.
High Reliability Organizations engage everyone, everywhere, every day in seeing, solving, and sharing risks. The only acceptable goal for harm is a High Reliability Organization is zero.
Questions for Reflection
So, here are a couple of questions to reflect on in your own organization. When does your organization typically take definitive action in the event of harm? How well do employees within see risk or vulnerabilities in processes, policies, physical space, behaviors and training that have the potential of generating harm?
Does your organization set a target for harm that accepts something higher than zero? If so, what message does this potentially send your employees and customers about accepting the risk of harm in the workplace?
Thank you for joining me today. For more information on Value Capture and safety in healthcare, please visit our website at valuecapturellc.com.
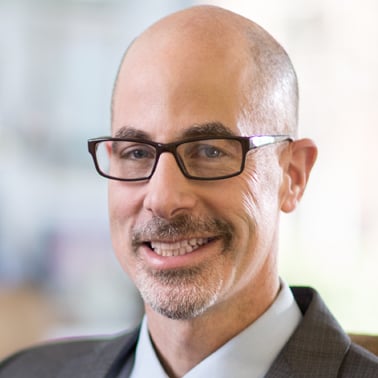
Submit a comment