Listen:
Scroll down for a transcript, how to subscribe, and more
Episode Synopsis:
Welcome to Episode #13 of Habitual Excellence, presented by Value Capture.
Joining us today is Steven J. Spear, a Senior Lecturer at MIT's Sloan School of Management and Senior Fellow at the Institute for Healthcare Improvement. His book, The High Velocity Edge, has won the Philip Crosby Medal from the American Society for Quality (ASQ) in 2011. Spear has a doctorate from Harvard Business School, a master’s in engineering and in management from MIT, and a bachelor’s degree in economics from Princeton. He's also the creator of See to Solve and is principal in his firm HVELLC.
Today, host Mark Graban talks to Steve about his experiences working with, and learning from, Paul O'Neill during his time as CEO at Alcoa. Steve connects important dots between organizations like Toyota, the U.S. Navy, Alcoa, and healthcare organizations that are seeking habitual excellence. How can we learn and evolve rapidly in this era of Covid-19? They talk about this and more, in an episode that was recorded in mid May.
Watch on YouTube
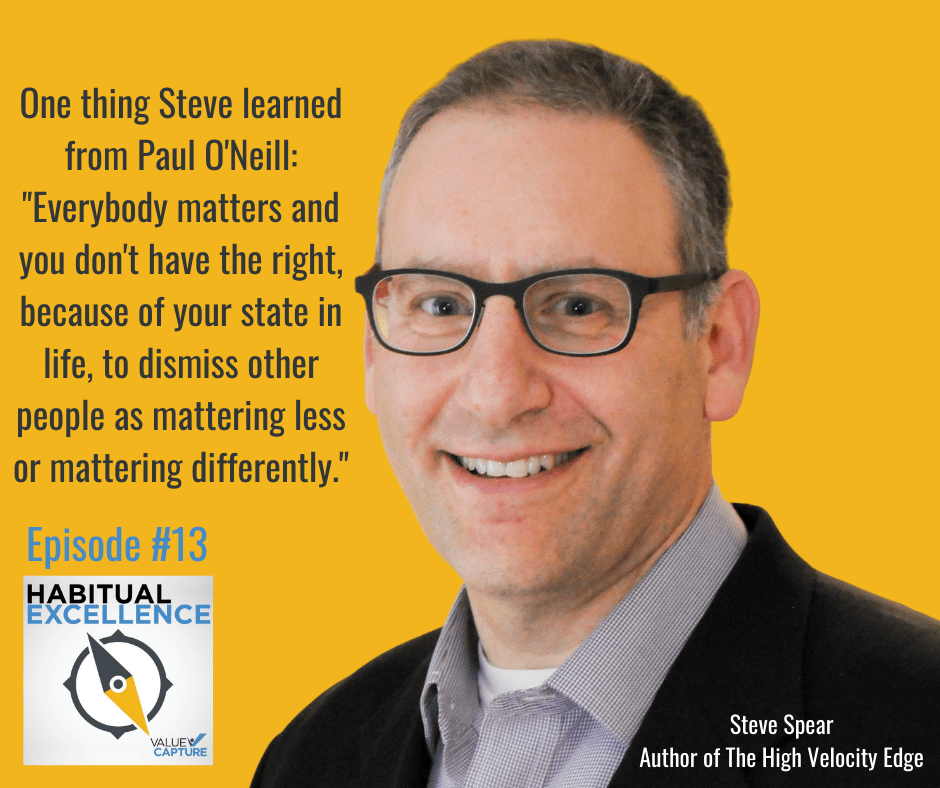
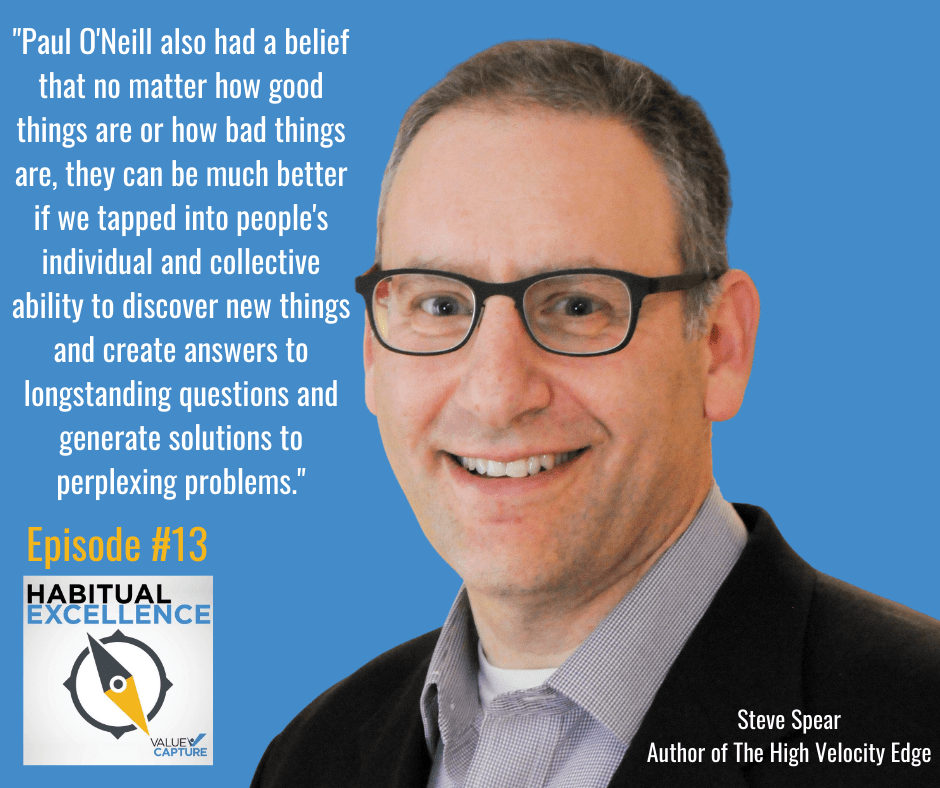
Click to visit the main Habitual Excellence podcast page.
Subscribe:
To make sure you don't miss an episode, be sure to subscribe today! Please rate and review the podcast.
Transcript:
Intro (2s):
Welcome to Habitual Excellence presented by Value Capture. This podcast and our firm is all about helping you and your organization achieve habitual excellence via one unifying focus, one value based structure and one performance system. In other words, it's about helping you capture dramatically more value through achieving perfect care and perfect safety for patients and staff. To learn more about Value Capture and our services visit www.valuecapturellc.com.
Mark Graban (37s):
Well, hi, welcome to the Habitual Excellence podcast. I'm Mark Graban. We're joined today by Steve Spear. Steve, how are you?
Steve Spear (44s):
I'm doing great. Good afternoon.
Mark Graban (46s):
It's good to talk to you. Can you tell the audience, the viewers a little bit about what you do? You do a lot of things.
Steve Spear (53s):
Yeah, thank you. So by affiliation I've, I'm on the faculty at MIT in the Sloan School, having an advisory practice called The High Velocity Edge, which is the same title as my book. More generally, I think my career has converged to the singularity of advocating for the scientific method and unpacking that a little bit. My work started 20, 30 years ago, trying to understand why there were some organizations, Toyota in particular, which were just these fantastic outliers and their ability to harness the contributions of people towards common purpose create value and a Toyota was it wasn't actually still as the standard set set or in their sector.
Steve Spear (1m 44s):
But what we found in looking at Toyota was that they had constructed ideally all work as a series of nested experiments from which not only did they make the product or deliver the service they wanted, but they were constantly learning whether they succeeded and especially if they failed. And what we've discovered when we looked elsewhere is that other anomalous super performers took a similar approach is sort of a convergent evolution that even though they may never collaborate in thinking about their own personal management theory, they came to the same conclusion. And so I'd say the last 15, 20 years I've worked with organizations of a fairly broad variety .com .edu .org .mil, trying to look for opportunities to build this very, very rich feedback environment by which every day, not only you doing the, the work that sort of your title or role suggest, but also you're creating useful knowledge that has a longer term application.
Steve Spear (2m 55s):
So yay science.
Mark Graban (2m 60s):
it's a good thing, obviously much needed. And a part of the approach of Paul O'Neill, you know, the co founder of Value Capture was an advocate for, you know, problem solving and the scientific method in our work and so much more. But, you know, as he passed away in April, you know, in his mid eighties, you know, he had been he'd left Alcoa where he'd been CEO until 2000. He was in the George W. Bush administration for a year and a half, almost two years, his treasury secretary. And, you know, a lot of people may have lost track of what he was doing since.
Mark Graban (3m 43s):
And you worked with him, you knew him a long time, so we'd be good to hear some of your stories and reflections on some of those things you collaborated on and what you learned and what you'd like to help pass on.
Steve Spear (3m 56s):
Yeah. So let me start with the pass on first, I think, and again, it's a shame, Paul was a national treasure. I think it's no exaggeration, probably an understatement to say there are tens of thousands of people who lived and are living much better lives than they would have because of his influence and not an exaggeration. And probably damning him with faint praise by saying it that way, Paul, to, to really boil down as parsimonious as I can make.
Steve Spear (4m 37s):
It had two key beliefs that I absorbed from him. I think he probably had others and I probably was too dense to absorb them. But the ones I absorbed from Paul were one that everybody matters and you don't have the right because of your state in life to dismiss other people as mattering less or mattering differently. And I think probably tightly coupled to his belief that everybody matters. Paul also had a belief that no matter how good things are or how bad things are, they can be much better if we tapped into people's individual and collective ability to discover new things and create answers to longstanding questions and generate solutions to perplexing problems.
Steve Spear (5m 31s):
And just as a quick summary, as to why I feel I have right to have such conviction and sort of summarizing them that way, I probably had met Paul so it had been 20 plus years ago. I was completing my studies as a doctoral student and trying to unpack or decode Toyota's DNA. And we came to this realization that Toyota was this unique organization or certainly unusual organization that viewed its management system as existing to tap into the problem solving ability of people so they could better meet society's needs.
Steve Spear (6m 16s):
And it happened to be that those needs were transportation needs, but they really viewed their management system and still do as this mechanism for tapping into people's innate potential. And while we were doing this work with Toyota, Alcoa under Paul's leadership was making this a real concerted effort to achieve a perfect workplace safety. And wouldn't, you know, that the approach they were taking was so in concert with Toyota's approach, that it created the opportunity for conversation and collaboration. So Paul and I, our relationship goes back to the late 1990s continued while we helped try to stand up the Alcoa business system within the company, after his retirement and extended to his being champion of the healthcare initiative in the Pittsburgh region.
Steve Spear (7m 13s):
And our relationship continued both during and then after when he was secretary of the treasury. So anyway, that's just some background to back up the claims I was making
Mark Graban (7m 28s):
Do you have some thoughts on, you know, cause I've heard different versions of story as the story from different people of how Alcoa had sort of gone on a search to find partners to learn from. And it seemed like that turned out being a Toyota and Harvard business school and that there were kind of, you know, mutual interests and learning in all directions. There is that fair to say?
Steve Spear (7m 53s):
Yeah, that's fair to say. So I've had like remarkably good fortune good luck. And I'd say finding mentors, it's not even that having people who, for whatever reason chose to mentor me and amongst those, you know, certainly I just fell into the opportunity to learn from Clay Christiansen for at least a decade. He was on my committee when I was doing my dissertation. He was senior faculty in the same group where I was junior faculty for six years. And he had a huge influence on me, another guy who, again, just, you know, the dumb coincidence that I happened to be in the right place where he was at the right time.
Steve Spear (8m 42s):
And he decided it was worth his time to develop me as a, as a scholar and a person who was Kent Bowen. And just to, you know, give you, you know, some real put Kent in some perspective, he was a brilliant enough early enough to have a full career achieve full tenured status at MIT and retire as professor emeriti at MIT joined the Harvard faculty in the business school and have a full career long enough to retire as professor emeritus at Harvard. I, you know, guy's freaking brilliant.
Steve Spear (9m 21s):
And it turned out that Kent, before he became a management theorist was one of the world leaders in ceramics. And I think it was by the coincidence of Kent having a very long standing relationship with some of the geniuses at Alcoa in the material sciences. Then when we started looking at Toyota connections, he had on very different topics, became the, the doorway for us to start having conversations around management theory too. And it turned out that at Alcoa, there was a guy also a savant, this guy, Keith Turnbull, who was curious about this stuff and, you know, by good coincidence was Paul O'Neill's emissary and representative on these topics.
Steve Spear (10m 10s):
So anyway, that's kind of the, the connections.
Mark Graban (10m 15s):
Yeah. So you've featured, or, you know, one of the organizations you featured in your book, the high velocity edge was Alcoa. I was wondering what, you know, what are some of the common threads that connect these different organizations like Alcoa and Toyota and the US Nuclear Navy and commonality, if you could talk about that.
Steve Spear (10m 40s):
Yes. So in terms of like nerding out in this, you know, unpacking, you know, so, you know, science often starts with trying to explain the anomaly and the references you just made to Toyota, Alcoa and the Navy's a reactor program or anomalous by enormous means. So let me just qualify, quantify that a little bit. So Toyota came to the attention of US managers, US academics, I guess in the mid eighties, when after a few years in the US market, they just started grabbing enormous amounts of share and putting the fortunes of the big three in a great predicament.
Steve Spear (11m 25s):
And the reason was quite simple was that Toyota was able to deliver cars at a far more affordable price with a much higher reliability level than anyone else in the world. And in terms of affordability piece, for example, Toyota's productivity was probably double, no matter how you measured it, it was double what was the world standard. So that was one anomaly and we can go into it. They still maintain their anomalous behavior in a very, very difficult competitive sector, Alcoa the connection there was, they were another one of these anomalous examples in a very, very different setting, right?
Steve Spear (12m 8s):
So heavy industry versus the discrete part manufacturing, et cetera, et cetera. But what they had done is take these industrial processes, which are so hostile to the wellbeing of human beings. Melt point of aluminum is well over a thousand degrees Fahrenheit, the crush pressure on a, on a die, extruding doorframes and window frames, you know, who knows how many thousands of pounds per square inch. I mean, these are processes designed in such a way that they're completely incompatible with human wellbeing and yet Alcoa had figured out their processes so well that they were the safest employer in the country, you know, and not like the safest heavy industry, you know, of, you know, it wasn't like amongst other people working with molten aluminum or molten metal, they were just the safest safer than libraries, consulting, firms, hospitals, et cetera.
Steve Spear (13m 6s):
And then the third example you mentioned is the US Navy's reactor program, which I'm sure are thinking about the proposition. I mean, this is screw it. Right. All right. So first of all, take radioactive material, put it into an engine, all right. Run that engine. So it generates, you know, ungodly amounts of electricity take that same engine, which we all know is difficult enough when you put it on land, put it inside a ship, sink the ship, and have the ship driven around by a crew, which in the day of a hundred, 150 people on board were all young men. And oh, by the way, don't give him any windows. And, and when I try to impress upon people about how cockamamie a proposition it is, I said, you know, if you're not at all queasy with the idea of men in their late teens or early twenties, driving around at top speed at a nuclear powered submarine, go home tonight, hand the keys to your newest car, to the local teenager and blindfold him.
Steve Spear (14m 10s):
And how do you feel about that? So, anyway, the reason I bring that up is that the Navy, that program took the idea of nuclear propulsion from just like, Oh, that's a good idea. When the science didn't exist, the technology didn't exist. They brought it into practice in this completely anomalous way. Is that not only did they get, get to market before the Soviet Navy, but since the launch of the USS Nautilus in the mid fifties, the Navy's experience, the nuclear power has been perfect, no reactor failure that's led to human harm or, or ecological damage. And you can't find anybody else has done the same thing.
Steve Spear (14m 51s):
So anyway, you know, why juxtapose Toyota Alcoa and Naval reactor program in the same book, it's because they've done the same thing. They've taken, what everyone else takes for granted as the constraints, et cetera. And the hazards of a sector is proven that those are actually the limits of that type of work.
Mark Graban (15m 13s):
And you know, this, this idea of a perfect safety track record, you know, it makes me think of something, Mr. O'Neill talked about a lot, the, the idea, the values based idea that, you know, nobody should ever get hurt when they go to work. I've heard of one of his former colleagues say that that had actually evolved to the idea that people should leave work healthier than they were when they arrived in the morning. But this idea of thinking of zero harm and what he called theoretical limits, where does that fit into your mind, the habitual excellence equation, how important is that?
Mark Graban (15m 53s):
And how do leaders help theoretical limits not just become a slogan, but actually turn into something actionablw.
Steve Spear (16m 3s):
So a couple of things here to unpack. So Paul was an interesting guy in the sense that when you asked him a question, he'd give you an, an answer. He wouldn't give you two answers to give one answer in which both the ethical and the rational were tightly integrated. And I never figured out a way to separate the two and in my recounting, because I don't have his eloquence, it sounds like they're separate, but they weren't for him. And so this issue about how someone arrives, you know, Paul's view was that if someone were willing to give you a day of their life to do something that you found valuable, right, you were willing to pay them because what they were doing was valuable to you, then you didn't have the right to put them at risk.
Steve Spear (17m 3s):
And again, that seems sort of contradictory to the whole idea of creating value through the use of things that are molten metal and, you know, pressures and velocities like we were discussing, but he started there. And then he continued the thought and which was, if you are introducing risk into their, into their life and at their wellbeing, then the reason you're doing that, either you're malicious and, and he didn't characterize himself, or his colleagues that Alcoa as malicious or the other possible reason you're introducing the risk is cause you certainly don't know. You don't know any better that if you knew perfectly about what to do, the risks, wouldn't be there.
Steve Spear (17m 45s):
Now just pausing a it's really such a profound statement because so often people say, well, you know, Mark, you know, you got to understand with all due respect, with all due respect, you know, this is an inherently dangerous thing to do. And Paul's attitude was that it's not written into the fabric of the universe, that this is a dangerous thing to do. And the reason it's a dangerous thing to do is we just don't know how to do it in a way that's not dangerous. And so the reason it's dangerous is that's all we know how to do. And so this led into, Paul's a set of ideas about how do you persuade people that whatever they're doing, remember I said earlier, you know, what was the core values that everyone matters?
Steve Spear (18m 29s):
All right. So someone, you don't have a right to put someone at risk because everyone matters and that things could be much better. So why are they at risk is because you don't know any better that all you know is how to put them at risk. If you didn't, if you knew how to not put them at risk, you wouldn't put them at risk. So anyway, this idea of theoretical limits played within the Alcoa environment into this pursuit of safety in this sort of impetus to learn because Alcoa is obviously a very process, intensive company, a lot of chemistry, a lot of physics. And you can actually do, like you did in high school chemistry, you can do your conservation of mass and energy calculations as to how much energy and mass you have to put in to get, you know, X number of doorframes and window frames out, or soda cans or whatever else.
Steve Spear (19m 20s):
And so there you have, what are the equation you wrote into your lab book and what the, the accountants told you, you actually spent to get your soda cans. And it was like, well, you know, you have this much soda can and, this is much you put in. So where'd all the other stuff go. And the answer was, it got dissipated by ignorance, because if you knew perfectly how to turn energy and material into soda cans, there'd be all, you have the soda cans, you wouldn't have this dissipation. The value is somewhere. So they use this idea of a theoretical limit as a way to keep provoking people and say, you know, if someone said, Hey, promise Ronnie or whomever else, you know, Mark, we've, we've optimized this process.
Steve Spear (20m 4s):
They say, well, let's calculate the theoretical limit. And it's like, Aw, crap. You know, but he never worked anywhere. It'd be like saying, Oh, this is as fast as it can go. Like, well, are you at the speed of light? Cause that's as fast as you can go. I was like, no, I'm not, no nowhere near the speed like, all right, go back and learn something else. So that's how some of those ideas tied together.
Mark Graban (20m 26s):
But you know, you're talking about that mindset of, yeah. Well, as you know, people have this resignation or acceptance that, well, this is a dangerous industry and its sad. Right? I wish it didn't happen, but it's what can you do? What can you do? Well, we don't know yet. Right? I think you articulated this really well. We've got to do something now. I want to talk a little bit about lessons that you might have for health care. Because I think sometimes there is a similar sort of self-defeating mindset of, well, you know, patients are just, it's sad and we wish it didn't happen, but some patients are bound to fall or, you know, our patients are sicker and they're bound to get infections.
Mark Graban (21m 6s):
This is nature. This is medicine. This happens. And, and you know, some people I know you've run across and worked with have realized, well, no, we don't have to just accept that. What can we do about it? That's the question. Let's do something, right. Yeah. What are your thoughts for healthcare around this?
Steve Spear (21m 24s):
Right. So there's, I suppose good reason for people in healthcare to be accepting of the imperfections patients and care providers experience in the course of a care being provided, the stakes are very high. Sometimes the lead times are very short. The situations can be very complex and the situations are fragile. I mean, you're dealing people who are less than in perfect health. And so when things go wrong, you have a lot of built in excuses.
Steve Spear (22m 6s):
Again, you know, the compressor, complexity, fragility, lack of lead time, et cetera, When, when you start, All right. So I understand the appeal of that argument, but it has two grotesque weaknesses. The first is empirical and the other is sort of, what's the word empierical not theoretical, but anyway, you can, you know, based on reason. So the empirical evidence, this is that some people have taken those situations, which are complex and fragile, et cetera, et cetera. And they've made them perfect. You know, they had central line infections, boom, no central line infections.
Steve Spear (22m 47s):
That was an experience we had working together at Allegheny general hospital with Rick Shannon, you had surgical site infections, boom, no surgical site infections. That was an, that was an experience or a transformation one by the folks at the Pittsburgh VA, you had patient falls. Patients don't fall anymore. You have bedsores, you don't have bed ulcers. You know, you don't have ulceration anymore. So you have the empirical evidence that these things which are taken for granted are solvable, but then he started getting into the logical. How is that possible? Well, the thing about these failures, which impact the wellbeing of staff and of patients is that no one ever gets hit by a meteor, right?
Steve Spear (23m 30s):
It's not like, Whoa, where did that come from? When you start doing the, the retrospect of the postmortem on these things, what you discover is that the reason harm was done was the accumulation of a lot of small or regular flaws in the system that in the moment somehow amalgamated to create a harmful situation. So a bunch of years ago, this guy, Mark Schmidthoffer, and I wrote an article in annals of internal medicine. The animals had, you know, the animals had done a series of case studies of care, gone, bad medical misadventure.
Steve Spear (24m 10s):
There was the guy who went into the emergency department and he literally fell through the cracks for about 10, 12 hours of getting paid pain. Untreated. It was a patient who got an invasive procedure. Her name was Mrs. Morris. She got one intended for Mrs. Morrison. There was a patient, you know, we wrote about a case of a patient who instead of getting a dose of heparin as an anticoagulant on a central line, ended up getting several doses of insulin, which ultimately led to her demise. And as we started to untangle, these cases, what we found was tolerance for lots of little things, which clearly were wrong, but because individually they never were severely wrong.
Steve Spear (24m 53s):
People said, hh, well, you know, that's just the nature of the beast. If you pick up the wrong vial and medication, well, put it back, be careful next time. If you get the wrong patient and give the wrong instruction, you know, alright, you know, correct for that in the moment, but be more careful next time. And it turns out be more careful. It's just horrendous line of defense. I mean, is that an awful line of defense against things going bad? And you know, it's funny because you think about our immune system, we, our immune system goes it's, first of all, it sets up barriers against infectious disease, you know, and that's why we have such, you know, resilient skin and we filter air as it goes in through our noses, et cetera, et cetera.
Steve Spear (25m 34s):
And then our immune system work at that moment that an infectious agent that the moment hits our system, you know, and it's just on the periphery. The immune system kicks in. It wants to get it before it has a chance when it's still just sort of probing before it has a chance to penetrate. We all know if we've had the experience of having a vulnerability, let's say a paper cut. And the infectious agent has penetrated. The immune system reacts to that with swelling, with bleeding, with losing whatever else it is to contain the problem. So it's sort of a, an odd irony that the people in healthcare deal with the object of their intention, these biological systems with these wildly involved mechanisms for seeing little problems early and addressing them before they have a chance to escalate.
Steve Spear (26m 30s):
And in fact, a lot of medical care, right, is trying to either compensate for the absence of those mechanisms or restore them if they've somehow broken. But then you have these organizational systems which don't have the same attributes and not only don't, they have the same attributes. There seems to be too often the lack of aspiration to have those attributes of a healthy immune system. And so anyway, you know, pushing back on that sector, when there's evidence, there's a science, which says much better as possible, and not only much better about it, much better and much easier. The other part is kind of the logic of the argument, which is, you know, COVID-19 is a pain in the butt right now, but by and large, you know, if it weren't, COVID-19 in the moment we're being attacked by who knows how many billions of microorganisms right now, trying to conspire for our demise.
Steve Spear (27m 23s):
And we don't care because we've got immune systems, which fend them off. So yeah,
Mark Graban (27m 30s):
But what, what would you hope to see ahead for us in healthcare? And I realize you might've had, you know, I don't know how much that answer changes because of what we've seen happening in healthcare with, with COVID-19. But if you, Well, I mean maybe a way of asking it is, you know, if you had a couple recommendations Leaders that you wish would be followed widely and diligently, what would some of those recommendations be?
Steve Spear (28m 3s):
Actually, Mark this is entirely thinking out loud, but I hope that the experience with COVID-19 is an inspiration for what really can be possible because you start thinking about this in, in January, you and I had no idea what COVID-19 was. I mean, maybe there was something going on in Wuhan, but did you and I discuss it. I don't think it was part of our conversation even in February. And I may, I may get the dates and times, not exactly precise, but more or less in terms of the flow. Maybe in February we say, well, man, they got a mess in Wuhan. I'm glad I'm not in Wuhan and you know, too bad for them, but you know, good, good for us. We don't have that problem. And then, Oh, by the way, we're going to, you know, no travel from China. Well, that seems prudent. Right? And then now there's like, I remember when this first became part of the president's conversation, he was having a Rose Garden or some other kind of press conference and a couple of the guests, you know, how they were going to deal with this, you know, rather than shaking his hand, they elbow bumped them.
Steve Spear (29m 0s):
I mean, and that seemed to like the extremist response to this thing, I said, Oh, we're going to shake hands. I'm going to bump elbows instead. And now we've been in two months, a lockdown, you know, 20 million people are out of work. The economy has shut down. We walked down the block and you think people are radiating something, you, you, you don't even look at people. Right. You know, I feel like we're in a horror movie now like that you see the movie, the, the bird box anyway. But yeah. It's like, Oh, you know, don't look out the window. You know, I get you. I mean, you know, so this thing came on us very quickly. Now you start thinking about what's going in healthcare, which is I'm confronted with this problem of what is it, what do we do?
Steve Spear (29m 48s):
How do we detect it? How do we treat it? How do we contain it better enough? The healthcare community and the public health community have been evolving, their understanding with blinding speed, which is why in January, you know, a lot of people didn't even know where Wuhan was. And here we are in April and May and people are locked inside their homes. And you know what, I'm confident by June and July, we'll be out doing something routine and our new normal. So anyway, where does that come from? Is that individually and as a community of medical professionals, public health professionals said, we have situations which are clearly a suboptimal really they're disastrous. And we don't know what to do. So what we are going to do is rather than just throw our hands up in defeat and rather than go back to old routines because they are not adequate.
Steve Spear (30m 35s):
What we're going to do is invent stuff, test it out the stuff that works, want to tell people about it and stuff that doesn't work. We're going to not exactly discard it. We're going to say it didn't work, but we've learned something from it, not working. And so we're going to move forward. Anyway, you start thinking about the learning dynamic that is going to get us from the severe collapse of the economy in April, to what I hope and even have some expectation will be recovery July, August, September. Where does that come from? It's this relentless dynamic of discovery and who unleashed and allow that dynamic of discovery.
Steve Spear (31m 16s):
It's the leaders in healthcare who said, Oh, these are the kinds of problems we can address. So anyway, you asked me what my hope is coming out of. This is that they don't let up. They said, you know what? All right, well, COVID-19, we got under control, but a wrong side surgery. We don't, but let's treat that the same way. And a surgical site infection. We don't have that one under control, but let's treat it the same way as COVID-19, let's get let's let's attack the problem with this laser, like focus on learning about it every day.
Mark Graban (31m 47s):
Yeah. I think that that is a really inspirational thought around as you put it evolving and learning rapidly. I have a friend who's an ER, doctor who's said over the last two months, how much the emergency medicine community has learned about responding to patients, how much the, the intensivists and the other specialists who are in the ICU have learned, and their treatments have evolved rapidly as they've learned. And it sounds like a lot of this happens through, you know, various networks, you know, formal and informal, right. You know, I think, you know, back to something you talk about and Value Capture has learned from you of, you know, we, we, we need to see solve and share, and we've seen this massive problem of coronavirus COVID-19 and people are solving things and they're sharing with each other.
Mark Graban (32m 40s):
Right. And it would be great to see more of that related to issues that they, you said is going to be their pressure ulcers, hospital, acquired infections, post surgical infections, wrong side surgeries, medication, dosing errors. How do we evolve and learn rapidly instead of repeating the same mistakes? It seems sometimes over and over again.
Steve Spear (33m 3s):
Absolutely. So, Mark, I think that the, the necessary transition here and you see it in a lot of places where people are doing signs, being quite literal in the metaphor, and in order to do signs, they got a, a lab bench and near like wickedly inquisitive and wickedly experimental on the thing on the lab bench. Now behind in order to do the work on the lab bench there's instruments. And while everyone is incredibly experimental about the object on the lab bench, some people not everybody are experimental about the instrumentation itself. Oh, what if I tune it this way?
Steve Spear (33m 44s):
What if I tweak it that way? What if I try to use it from this different configuration? When you go from the lab bench to the instrumentation, to the enterprise, we lose our bias towards experimentation. But if the thing on the lab bench is a complex dynamic, unknown, and the instrument we're using as a complex dynamic, unknown, certainly the enterprise, which is trying to engage the efforts of dozens, if not hundreds, if not thousands of people using all that complex stuff, that that's a complex dynamic unknown also. But for whatever reason, the people who train up in the sciences and in engineering and all these other disciplines, which advocate for, and reward the curious mind as they get further and further and further and further away from the, the lab bench and more and more where the responsibility is not the bench on the instrument, but the enterprise, the bias towards experimental inquiry and discovery it dissipates.
Steve Spear (34m 56s):
And I think that's an unfortunate consequence of too many decades of telling managers that their job is to lead by setting objectives or to give commands, and then audit for compliance or to manage by, you know, combination against setting objectives and having metrics kind of an up or out like with Jack Welch back in the day. And it's unfortunate because I think it obscures the reality that these social constructs called organizations also have a tremendous amount unknown and a tremendous amount about them, which can be discovered if we had the same inquisitive intent we have for what what's on the bench top or the work bench.
Steve Spear (35m 51s):
So anyway, I, I do hope that there's some reminder and some recollection coming out of his COVID crisis, that this is just how we should conduct ourselves. And it's not just, Oh, we're done with that. And now back to our routines and which break all the time, but we work around those problems.
Mark Graban (36m 17s):
Well, well, said and really a lot to think about. So thank you, Steve, for thinking out loud and sharing your thoughts. It's really helpful to hear,
Steve Spear (36m 27s):
Oh, you're quite welcome. And Mark, I do appreciate the chance for you to roll out the soapbox for me to stand on and rant and rave, you know, cause I I've been with my family for the last two months and I think they're kind of a little sick of that framing up from their own perspective, but you know, more, more seriously, I think the encouraging word here and really channeling what Paul's beliefs were, which is much better s possible. And we achieve much better, faster, the quicker we are to recognize what we don't know and can do and get on with it. And well, I'll tell you, he was not a man of excuses, you know, and not a man of the word excuses.
Steve Spear (37m 11s):
If something was bad, it was bad and it was bad. And not only did it need to be fixed, but it could be fixed. So get on with it. And I think there's something to be said for that
Mark Graban (37m 23s):
One phrase to use a lot as I've been reviewing his, some of his speeches and recordings and we're, we're putting some of those into an ebook to capture that for people who want to take it in that way, he would say the role of leaders is to remove excuses, right? Why, you know, why he talked about, you know, as you alluded to earlier, we're gonna have zero harm at Alcoa and people would give him all the reasons why that wasn't likely or wasn't possible and say well, through all of leaders is to help people eliminate those excuses and learn how figure out that better way,
Steve Spear (37m 58s):
You know, and Mark I think that's a great one because what Paul said, couldn't be confused with these stupid cliches, but in his case they were neither cliches nor stupid. So one is a, Oh, I don't want problems. I want answers. Well for the manager who says that, who only wants answers, not problems. It's like, what the hell is your role? Yeah. I mean, if everyone has the answer, why didn't you even exist? Why do you even have a job country club membership? I think what Paul was trying to get to is he wanted problems, but what he didn't want was you to explain to him why the problem had to exist.
Steve Spear (38m 40s):
He wanted a path forward to make the problem disappear and the, the thing he wouldn't be tolerant of, and he wouldn't allow you was the excuse as to why you couldn't try to move forward and anyway, really different from the cliche. It might've sounded like.
Mark Graban (38m 60s):
So Steve, thank you again for sharing thoughts and reflections here. I do want to mention again for the listeners and the viewers, I really do recommend Steve's book the high velocity edge. You can find that on Amazon and find bookstores and Steve, if people want to come and learn more about your work, how w what's the best place to come find you online?
Steve Spear (39m 23s):
Yeah. Right now I think the, the best is we've got a, we've created some tools that support this high velocity learning dynamic. And so we've got a bunch of stuff posted it. The website is www.seetosolve.com. Not a lot of creativity on the, the browser name, And there's more information there.
Mark Graban (39m 51s):
That's probably good. You didn't get too creative with how to the letter C the number two, the ampersand.
Steve Spear (39m 58s):
No, no, no, no. seetosolve.com. Yeah. I'm a fairly literal linear person. So that would have been beyond my capability or my understanding, but again, our guest is,
Mark Graban (40m 12s):
has been Steve Spear. I want to thank everyone for listening and watching. And Steve, thank you for joining us here today.
Steve Spear (40m 18s):
All right, Mark. Thank you and much appreciate you spreading the word about all these good ideas that we often get to discuss.
Outro (40m 24s):
Thanks for listening to Habitual Excellence presented by Value Capture. We hope you'll subscribe to the podcast and please also rate and review it in your favorite podcast, directory or app to learn more about value capture and how we can help your organization on this journey to habitual excellence, visit our website at www.valuecapturellc.com
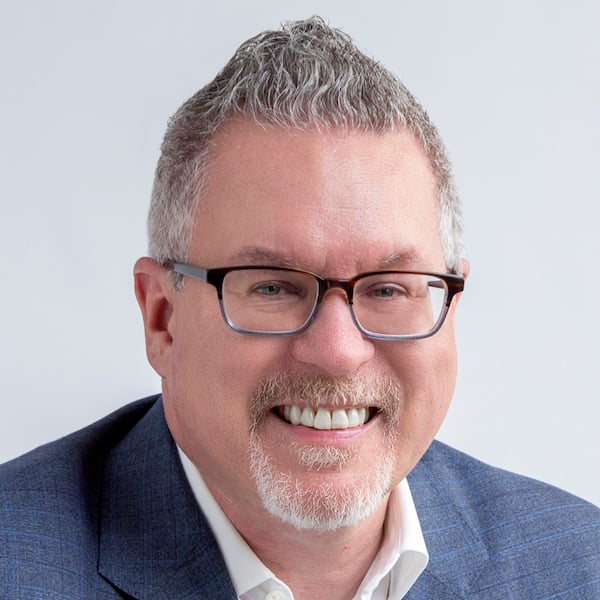
Written by Mark Graban
Mark Graban has served healthcare clients since 2005. Mark is internationally recognized as a leading author and speaker on Lean healthcare. His latest book is "The Mistakes That Make Us: Cultivating a Culture of Learning and Innovation."
Submit a comment